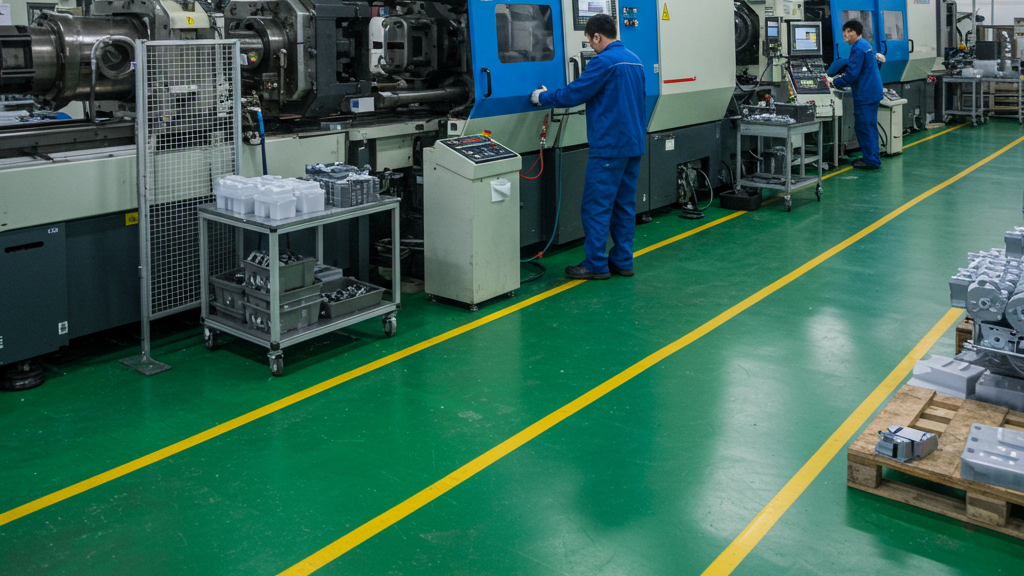
ABS (Acrylonitrile Butadiene Styrene) injection molding, as a mature polymer processing technology, has been widely used in the engineering field. Discussing the extent to which it can replace traditional metal materials requires a rigorous analysis from multiple dimensions, including material properties, application scenarios, and economics.
ABS exhibits significant differences in density, electrical conductivity, and high-temperature resistance. However, its excellent moldability, relatively low cost, and good corrosion resistance give it unique competitiveness in applications where material strength requirements are not high but lightweighting, design flexibility, and cost sensitivity are important.
What Metal Applications Has ABS Replaced?
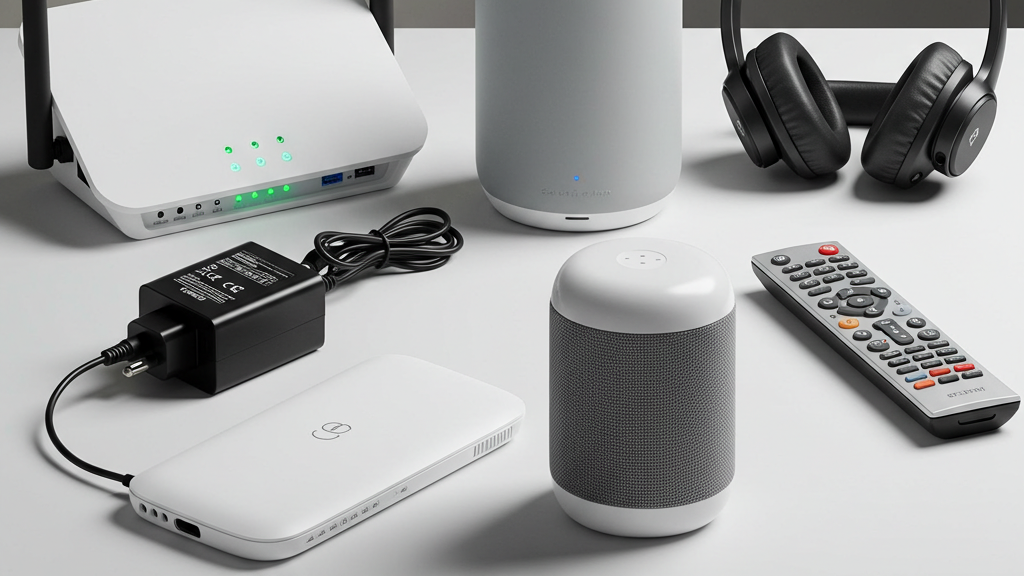
Exploring the penetration of ABS injection molding in various industries, one noteworthy focus is how it has quietly replaced the role of traditional metals in some areas. From daily necessities to industrial components, ABS seems to be ubiquitous.
- Lightweighting Applications in the Automotive Industry: Due to its lightweight and design flexibility, ABS is widely used in automotive interior and exterior trim. Some reinforced ABS materials can even replace semi-structural components in automobiles.
- Insulation and Aesthetics in Electronics and Electrical Appliances: Electronic and electrical equipment often use ABS to make housings and connectors due to its good insulation and ease of coloring.
- Toughness and Ease of Molding in Consumer Products: The toughness and ease of molding of ABS allow it to replace some metal parts in consumer products such as household appliances, toys, and tools.
- Biocompatibility and Corrosion Resistance in Healthcare: ABS’s biocompatibility and corrosion resistance make it suitable for equipment housings and components in the healthcare sector.
What are the Cost, Process, and Design Advantages of ABS?
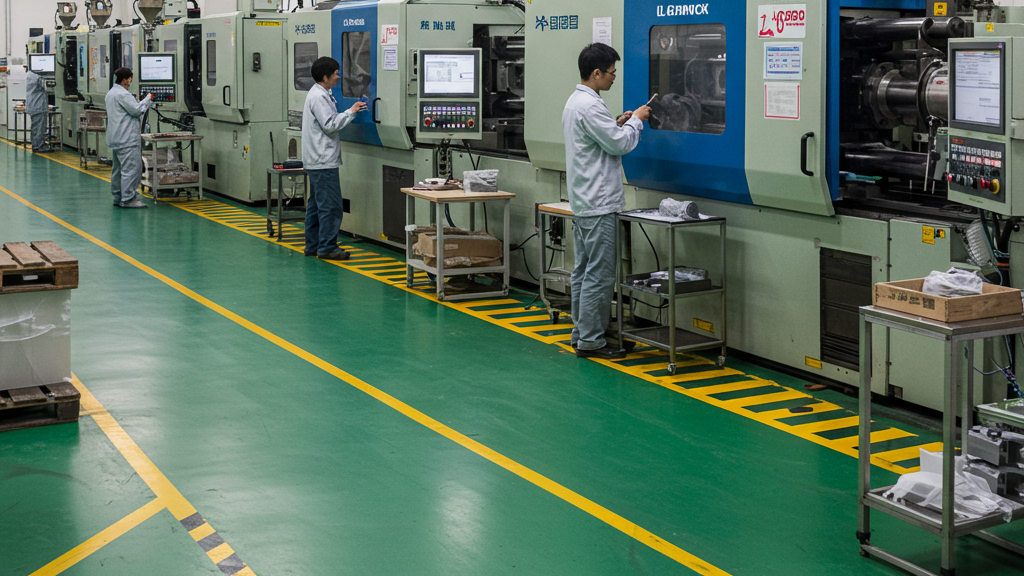
Compared to traditional metal materials, ABS injection molding often exhibits unique appeal in terms of cost control, production process flow, and design freedom. Economic efficiency and convenience, as well as flexible design space, make ABS a valuable complement or even a substitute option for metals in many application areas.
- Economical and Efficient Production: ABS raw materials and post-processing costs are typically lower than those of metals, and production efficiency and yield rates are high.
- Flexible and Efficient Process: Injection molding can integrally form complex structures, with short production cycles, high material utilization, and diverse surface treatment options.
- Free and Lightweight Design: ABS injection molding provides a high degree of design freedom, making it easy to achieve functional integration and lightweighting, and can optimize tactile feel.
- Wide Range of Colors and Surface Options: ABS resin itself can be colored, and injection molded parts can achieve rich colors and surface effects through mold design and post-processing.
What About the Strength, Heat Resistance, and Wear Resistance of ABS?
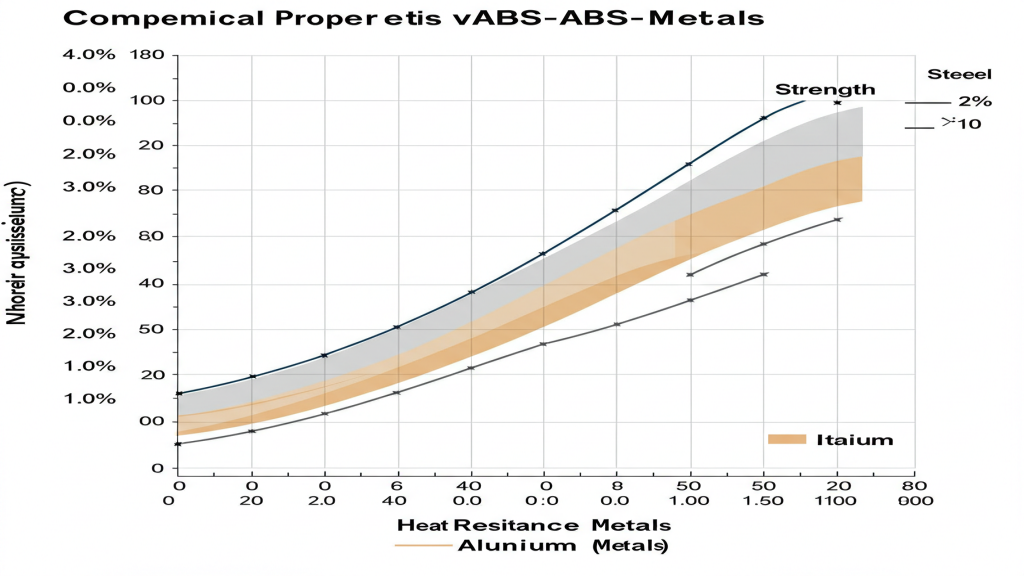
Although ABS injection molding exhibits many advantages in cost, process, and design, its strength, heat resistance, and wear resistance often become key factors in considering whether it can truly replace metals in some applications where material performance requirements are stringent.
- Strength and Toughness: ABS has moderate strength and rigidity, as well as good impact strength, but is significantly lower than metal.
- Limited Heat Resistance: ABS has poor heat resistance and is easily softened and deformed at high temperatures, limiting its high-temperature applications.
- Moderate Wear Resistance: The wear resistance of ABS is at a moderate level, not as good as most metals, and is not suitable for high-wear environments.
- Potential for Improvement Through Modification: The strength and heat resistance of ABS can be improved through modification, giving it the potential to replace metals in specific fields.
Comparison between ABS and metal materials in performance
Property |
ABS Injection Molding |
Steel (Carbon Steel) |
Aluminum (6061 Aluminum) |
Titanium (Grade 5) |
Strength | Medium (Tensile Strength 30-60 MPa) | High (Tensile Strength 400-550 MPa) | Medium-High (Tensile Strength ~310 MPa) | Very High (Tensile Strength ~950 MPa) |
Heat Resistance | Poor (HDT 80-100°C) | High (Withstands hundreds to thousands of °C) | Medium (Withstands ~150-200°C) | High (Withstands hundreds of °C) |
Wear Resistance | Medium, Easily Scratched | Good to Excellent, Depends on Hardness | Medium, Not as Good as Steel | Good to Excellent, Corrosion Resistance Aids Wear |
Cost | Relatively Low | Low to Medium | Medium | High |
Density | Low (~1.05 g/cm³) | High (~7.85 g/cm³) | Low (~2.7 g/cm³) | Low (~4.5 g/cm³) |
Technologies to Enhance ABS Performance
By introducing reinforcing fillers, blending with other polymers, or applying surface treatments to the ABS matrix, the aim is to significantly improve its strength, rigidity, heat resistance, wear resistance, and other key properties. These advancements not only broaden the application boundaries of ABS but also enable it to meet more demanding engineering application scenarios while pursuing lightweighting, cost-effectiveness, and design flexibility.
1.Fiber Reinforcement Significantly Improves Mechanical and Thermal Properties: The addition of glass fibers and carbon fibers can significantly improve the strength, rigidity, and dimensional stability of ABS, and improve its heat resistance.
2.Elastomer Blending Enhances Impact Toughness: Blending with elastomers effectively increases the impact strength and toughness of ABS by enhancing the energy absorption capacity of the material.
3.Nanotechnology Imparts Multiple Performance Enhancements: Adding nanofillers to ABS can significantly improve its mechanical and thermal properties even at low concentrations, and even give it new functions such as electrical conductivity.
4.Surface Treatment Extends Application Adaptability: The use of surface treatment technology can change the surface characteristics of ABS materials to suit specific application needs, such as improving adhesion or wear resistance.
Conclusion
ABS injection molding has replaced some metals in many fields due to its cost, process, and design advantages. Standard ABS is inferior to metals in terms of strength, heat resistance, and wear resistance, which limits its application range. With technological advancements, modified ABS is expected to play an important role in a wider range of industrial fields.
For expert assistance in implementing for your production needs, visit our resource center or contact us. Let’s help you scale up your manufacturing with precision and efficiency!
Post time: Apr-08-2025